The Ultimate Guide to CNC Machining: Processes, Benefits, and Applications
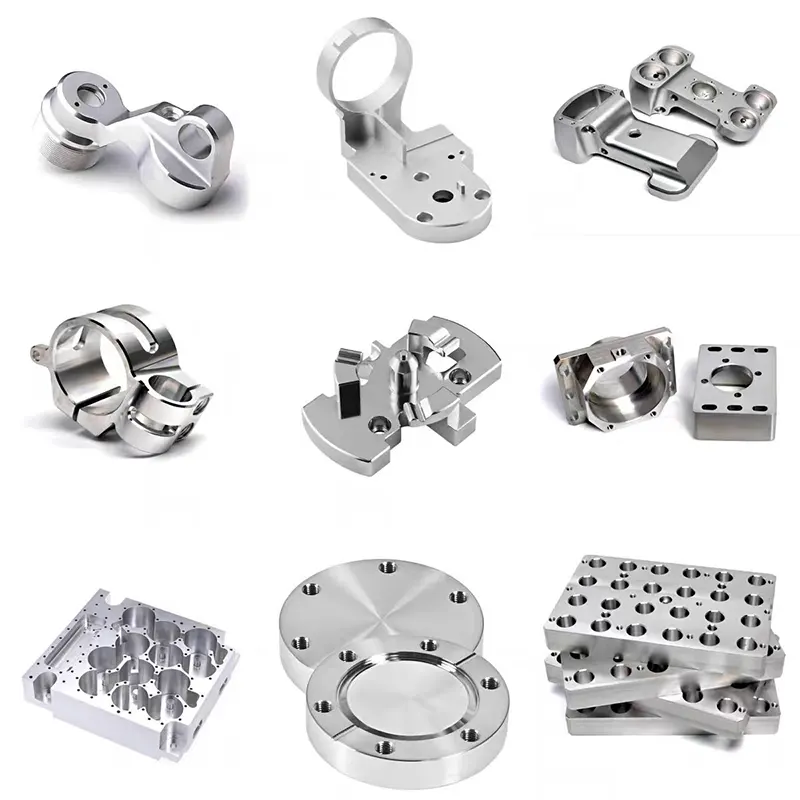
CNC (Computer Numerical Control) machining has revolutionized the manufacturing industry, offering unparalleled precision, efficiency, and versatility. From aerospace components to medical devices, CNC machining plays a critical role in producing high-quality parts and products. In this comprehensive guide, we’ll explore the processes, benefits, and applications of CNC machining, helping you understand why it’s a cornerstone of modern manufacturing.
What is CNC Machining?
CNC machining is a subtractive manufacturing process that uses computerized controls and machine tools to remove layers of material from a workpiece, creating a custom-designed part or product. Unlike manual machining, CNC machining relies on pre-programmed software to dictate the movement of machinery, ensuring consistent and precise results.
The process begins with a digital 3D model created using CAD (Computer-Aided Design) software. This model is then converted into a set of instructions (G-code) that the CNC machine follows to execute the machining operations. CNC machines can perform a variety of tasks, including milling, turning, drilling, and grinding, making them suitable for a wide range of applications.
Key CNC Machining Processes
CNC machining encompasses several processes, each tailored to specific manufacturing needs. Here are the most common ones:
1. **CNC Milling**
CNC milling involves rotating cutting tools to remove material from a stationary workpiece. The machine can move along multiple axes (typically 3 to 5), allowing for the creation of complex shapes and intricate designs. Common milling operations include face milling, peripheral milling, and slot milling.
2. **CNC Turning**
In CNC turning, the workpiece rotates while a stationary cutting tool removes material. This process is ideal for creating cylindrical or conical parts, such as shafts, bolts, and bushings. CNC lathes are commonly used for turning operations.
3. **CNC Drilling**
CNC drilling uses rotating drill bits to create holes in a workpiece. The machine can drill holes of various sizes and depths with high precision, making it essential for applications requiring accurate hole placement.
4. **CNC Grinding**
CNC grinding employs abrasive wheels to achieve fine finishes and tight tolerances. This process is often used for finishing operations, ensuring that parts meet exact specifications.
5. **CNC Laser Cutting**
While not strictly a machining process, CNC laser cutting uses high-powered lasers to cut through materials like metal, plastic, and wood. It’s a popular choice for creating intricate designs and patterns.
Benefits of CNC Machining
CNC machining offers numerous advantages over traditional manufacturing methods. Here are some of the key benefits:
1. **Precision and Accuracy**
CNC machines operate with exceptional precision, often achieving tolerances within ±0.001 inches. This level of accuracy ensures that parts are produced to exact specifications, reducing the risk of errors and defects.
2. **Consistency**
Once a CNC program is created, the machine can produce identical parts repeatedly. This consistency is crucial for large-scale production runs and industries where uniformity is critical, such as aerospace and automotive.
3. **Versatility**
CNC machining can work with a wide range of materials, including metals (aluminum, steel, titanium), plastics, composites, and wood. This versatility makes it suitable for diverse industries and applications.
4. **Efficiency**
CNC machines can operate 24/7 with minimal supervision, significantly reducing production time. Additionally, the automation of CNC machining minimizes human error and increases overall efficiency.
5. **Complexity**
CNC machining can produce highly complex geometries that would be difficult or impossible to achieve with manual methods. This capability is particularly valuable for industries like medical devices and aerospace, where intricate designs are common.
6. **Cost-Effectiveness**
While the initial investment in Cmachinery can be high, the long-term cost savings arNC e substantial. Reduced labor costs, minimal material waste, and faster production times contribute to a lower overall cost per part.
Applications of CNC Machining
CNC machining is used across a wide range of industries due to its versatility and precision. Here are some of the most common applications:
1. **Aerospace**
The aerospace industry relies on CNC machining to produce high-precision components like turbine blades, engine parts, and structural elements. The ability to work with lightweight materials like titanium and aluminum is particularly valuable in this sector.
2. **Automotive**
CNC machining is essential for manufacturing automotive parts, including engine components, transmission systems, and custom fittings. The process ensures that parts meet strict safety and performance standards.
3. **Medical**
In the medical field, CNC machining is used to create surgical instruments, implants, and prosthetics. The high precision and biocompatibility of machined parts are critical for patient safety and treatment efficacy.
4. **Electronics**
CNC machining is used to produce components for electronic devices, such as heat sinks, connectors, and enclosures. The process ensures that parts are manufactured to exact specifications, ensuring optimal performance.
5. **Prototyping**
CNC machining is widely used for prototyping due to its ability to quickly produce functional prototypes with high accuracy. This allows designers and engineers to test and refine their designs before moving to full-scale production.
6. **Consumer Goods**
From kitchen appliances to sporting equipment, CNC machining is used to create a wide range of consumer products. The process ensures that products are durable, functional, and aesthetically pleasing.
Choosing the Right CNC Machining Service
If you’re considering CNC machining for your project, it’s essential to choose the right service provider. Here are some factors to consider:
– **Experience and Expertise**: Look for a provider with a proven track record in your industry.
– **Material Capabilities**: Ensure the provider can work with the materials you need.
– **Quality Assurance**: Check for certifications like ISO 9001, which indicate a commitment to quality.
– **Turnaround Time**: Choose a provider that can meet your deadlines without compromising quality.
– **Customer Support**: Opt for a provider that offers excellent communication and support throughout the process.
The Future of CNC Machining
As technology continues to advance, CNC machining is poised to become even more efficient and versatile. Innovations like AI-driven automation, additive manufacturing integration, and advanced materials are shaping the future of the industry. These developments will enable manufacturers to produce even more complex and high-quality parts, further solidifying CNC machining’s role as a cornerstone of modern manufacturing.
Conclusion
CNC machining is a powerful and versatile manufacturing process that offers numerous benefits, including precision, consistency, and efficiency. Its applications span a wide range of industries, from aerospace to consumer goods, making it an indispensable tool for modern production. By understanding the processes, benefits, and applications of CNC machining, you can make informed decisions for your manufacturing needs and stay ahead in a competitive market.
Whether you’re prototyping a new product or scaling up production, CNC machining provides the precision and reliability you need to succeed. Embrace this cutting-edge technology and unlock new possibilities for your business.
CONTACT INFORMATION
- Xinyi.ouyang@ihktech.com
- +86 15323384821
- 910-A03,9th Floor, Building 9 (Building 8 #), No.6, Nanjiang Second Road, Zhujiang Street, Nansha District, Guangzhou
You May Like
Have Anything To Ask Us?
Please fill in the detailed information in the form, and we will contact you as soon as possible!