The Future of CNC Machining: Trends and Innovations to Watch
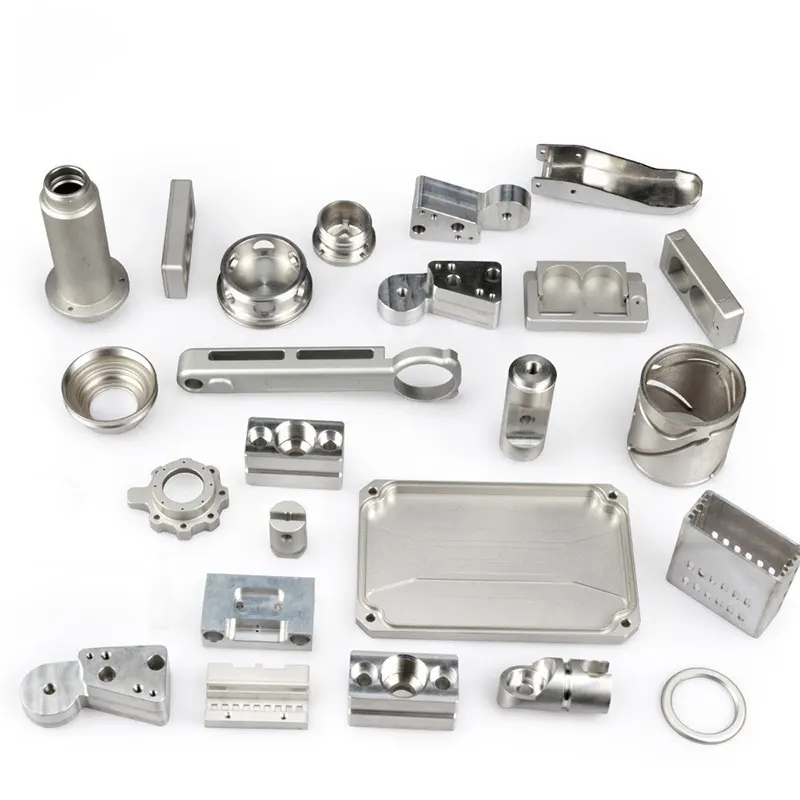
The world of manufacturing is undergoing a transformative evolution, and at the heart of this revolution is **CNC (Computer Numerical Control) machining**. As industries demand higher precision, faster production, and more sustainable practices, CNC machining is adapting to meet these needs. In this article, we’ll explore the latest trends and innovations shaping the future of CNC machining, and how they are poised to redefine manufacturing as we know it.
1. **Automation and Smart Factories
One of the most significant trends in CNC machining is the integration of **automation** and the rise of **smart factories**. Automation is no longer limited to simple repetitive tasks; it now encompasses advanced robotics, machine learning, and artificial intelligence (AI). These technologies are enabling CNC machines to operate with minimal human intervention, reducing errors and increasing efficiency.
– **Collaborative Robots (Cobots):** Cobots are designed to work alongside human operators, enhancing productivity and safety. In CNC machining, cobots can handle tasks like loading and unloading materials, tool changes, and quality inspections.
– **AI-Driven Predictive Maintenance:** AI algorithms can analyze machine data to predict when a CNC machine is likely to fail or require maintenance. This reduces downtime and extends the lifespan of equipment.
– **IoT-Enabled Machines:** The Internet of Things (IoT) allows CNC machines to communicate with each other and with central systems. This connectivity enables real-time monitoring, data collection, and process optimization.
The result? A seamless, interconnected manufacturing environment where machines, systems, and humans work in harmony to achieve unprecedented levels of productivity.
2. **Additive Manufacturing and Hybrid CNC Machines
The line between **subtractive manufacturing** (traditional CNC machining) and **additive manufacturing** (3D printing) is blurring. Hybrid CNC machines that combine both technologies are emerging as a game-changer in the industry.
– **Hybrid Machines:** These machines can perform both subtractive and additive processes, allowing manufacturers to create complex parts with intricate geometries that would be impossible using traditional methods alone.
– **Material Efficiency:** Additive manufacturing reduces material waste by building parts layer by layer, while CNC machining ensures precision and surface finish. Together, they offer a sustainable and cost-effective solution.
– **Rapid Prototyping:** Hybrid machines enable faster prototyping by combining the speed of 3D printing with the accuracy of CNC machining. This accelerates product development cycles and reduces time-to-market.
As hybrid machines become more accessible, they are expected to revolutionize industries like aerospace, automotive, and medical devices.
3. **Advanced Materials and Tooling**
The demand for stronger, lighter, and more durable materials is driving innovation in CNC machining. Manufacturers are increasingly working with advanced materials like **titanium alloys**, **composites**, and **ceramics**, which require specialized tooling and machining techniques.
– **High-Speed Machining (HSM):** HSM techniques are being developed to handle tough materials without compromising precision or tool life.
– **Diamond-Coated Tools:** For machining ultra-hard materials, diamond-coated cutting tools are becoming the go-to solution. They offer superior wear resistance and extended tool life.
– **Sustainable Materials:** The push for sustainability is leading to the adoption of eco-friendly materials like biodegradable plastics and recycled metals. CNC machining is adapting to work with these materials efficiently.
These advancements are enabling manufacturers to produce components that meet the rigorous demands of modern industries while reducing environmental impact.
4. **Enhanced Precision with 5-Axis and Multi-Tasking Machines**
Precision is the cornerstone of CNC machining, and the industry is pushing the boundaries with **5-axis** and **multi-tasking machines**.
– **5-Axis Machining:** Unlike traditional 3-axis machines, 5-axis CNC machines can move tools along five different axes simultaneously. This allows for the creation of highly complex parts with fewer setups, reducing production time and improving accuracy.
– **Multi-Tasking Machines:** These machines combine multiple operations, such as milling, turning, and drilling, into a single setup. This eliminates the need for transferring parts between machines, reducing errors and increasing efficiency.
As industries like aerospace and medical devices demand ever-higher levels of precision, 5-axis and multi-tasking machines are becoming indispensable.
5. **Sustainability and Green Manufacturing**
Sustainability is no longer a buzzword; it’s a necessity. The CNC machining industry is embracing **green manufacturing** practices to reduce its environmental footprint.
– **Energy-Efficient Machines:** Newer CNC machines are designed to consume less energy without compromising performance.
– **Waste Reduction:** Advanced software and machining techniques are minimizing material waste, while recycling programs are being implemented to reuse scrap materials.
– **Eco-Friendly Coolants:** Traditional cutting fluids are being replaced with biodegradable and non-toxic alternatives, reducing environmental harm.
By adopting sustainable practices, CNC machining is not only contributing to a greener planet but also appealing to eco-conscious customers.
6. **Digital Twin Technology**
**Digital twin technology** is revolutionizing CNC machining by creating virtual replicas of physical machines and processes.
– **Real-Time Monitoring:** Digital twins allow manufacturers to monitor machine performance in real-time, identify inefficiencies, and make data-driven decisions.
– **Simulation and Testing:** Before a part is physically produced, it can be simulated and tested in a virtual environment. This reduces the risk of errors and ensures optimal machining parameters.
– **Predictive Analytics:** By analyzing data from digital twins, manufacturers can predict potential issues and optimize production processes.
This technology is transforming CNC machining into a more agile and responsive industry.
7. **Customization and On-Demand Manufacturing**
The rise of **customization** and **on-demand manufacturing** is reshaping the CNC machining landscape. Consumers and businesses alike are demanding personalized products, and CNC machining is uniquely positioned to deliver.
– **Mass Customization:** CNC machines can produce customized parts without the need for expensive tooling changes, making it feasible to offer personalized products at scale.
– **On-Demand Production:** With the ability to quickly switch between jobs, CNC machining is ideal for on-demand manufacturing, reducing inventory costs and waste.
This trend is particularly evident in industries like consumer electronics, automotive, and healthcare, where tailored solutions are increasingly in demand.
8. **Workforce Development and Training**
As CNC machining becomes more advanced, the need for skilled workers is growing. The industry is investing in **workforce development** and **training programs** to bridge the skills gap.
– **Virtual Reality (VR) Training:** VR is being used to train operators in a safe and immersive environment, reducing the learning curve and improving retention.
– **Upskilling Programs:** Companies are offering training programs to upskill existing employees, ensuring they can operate the latest CNC technologies.
– **Collaboration with Educational Institutions:** Partnerships between manufacturers and schools are fostering the next generation of CNC machinists.
By investing in human capital, the industry is ensuring its continued growth and innovation.
Conclusion
The future of CNC machining is bright, driven by cutting-edge technologies and a commitment to sustainability, precision, and efficiency. From automation and hybrid machines to advanced materials and digital twins, the industry is evolving at an unprecedented pace. As these trends and innovations continue to unfold, CNC machining will remain at the forefront of modern manufacturing, enabling businesses to meet the challenges of tomorrow.
Whether you’re a manufacturer, engineer, or industry enthusiast, staying informed about these developments is crucial. The future of CNC machining is not just about machines; it’s about the endless possibilities they create.
By embracing these trends, businesses can position themselves for success in an increasingly competitive and dynamic manufacturing landscape. The future is here—are you ready to seize it?
CONTACT INFORMATION
- Xinyi.ouyang@ihktech.com
- +86 15323384821
- 910-A03,9th Floor, Building 9 (Building 8 #), No.6, Nanjiang Second Road, Zhujiang Street, Nansha District, Guangzhou
You May Like
Have Anything To Ask Us?
Please fill in the detailed information in the form, and we will contact you as soon as possible!